بررسی روند تولید پودرهای گرافیتی به عنوان روانکار دما بالا
گرافیت به دلیل ویژگیهای زیادی که دارد محصولات مختلفی از آن به دست میآید و این محصولات کاربرد فراوانی در صنایع دارد. یکی از این ویژگیها، خواص روانکاری آن است.
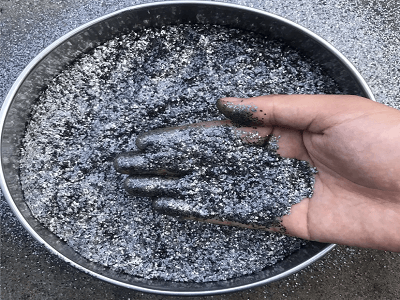
پودرهای گرافیتی خاصیت روانکنندگی بالایی دارد، از این رو سالها است که به عنوان روانکار خشک، برای جلوگیری از اصطکاک در دستگاههای صنعتی استفاده میشود. خصوصا در روانکارهایی که در دمای بالا میبایست استفاده شوند، روانکارهای پایه روغنی از بین میروند لذا روانکارهای گرافیتی کاربرد پیدا میکند. البته در کاربردهای روانکاری، معمولا این ماده در ترکیب با روغن استفاده میشود.
در بسیاری از کاربردها، روغن و کریستالهای لایه لایه گرافیت به تنهایی کافی نیستند. در این مواقع از افزودنیهایی مانند فلزات نرم (ایندیم، سرب، نقره، قلع)، پلی تترافلوئورواتیلن، بعضی از اکسیدهای جامد، فلوریدهای نادر زمین و حتی الماس به همراه گرافیت استفاده میشود. موارد استفاده از این روانکارها در فشردهسازی هوا، بلبرینگ، اتصالات سرعت ثابت، قفلها و غیره است.
انتخاب روانکار مناسب برای قالب، یکی از مهمترین و موثرترین عوامل در انجام فرآیند فورج موفق محسوب میشود. افزایش حداکثری عمر قالب، جلوگیری از گیرکردن و چسبیدن قطعات به قالب بخشی از مزایای و کاربرد گرافیت است.
روانکارهای گرافیتی
روانکارهای گرافیتی موادی با کاربردهای خاص در دماهای خیلی بالا یا خیلی پایین هستند. از این روانکارها برای مثال در روانکاری سطح قالبهای آهنگری و یک عامل ضدقفل شدن، به عنوان روانکار چرخ دنده ماشین آلات معدنکاری، و روانکاری قفلها استفاده میشود. با ترکیب فلزات با گرافیت میتوان آلیاژهای خودروانکار، برای مثال برای ساخت یاتاقانهای ماشینآلاتی که در دماهای بالا یا پایین کار میکنند، تولید کرد.
روانکنندهها چه مقدار در محیطهایی با حرارت بالا مهم هستند؟
انتخاب روانکننده مناسب در اطمینان از عملکرد بهینه بلبرینگ و جلوگیری از خرابی آنها بسیار مهم است. روانکنندهها، روغن یا گریس مانند یک لایه حفاظتی نازک عمل میکنند که از تماس اجزای بلبرینگ با یکدیگر و ایجاد اصطکاک جلوگیری میکند. اگرچه دلایل خرابی بلبرینگها بیشمار است؛ اما طبق تحقیقاتی که انجام شده است از هر پنج مورد خرابی بلبرینگها چهار مورد مربوط به روانکاری است.
روانکاری کردن بلبرینگها نسبت به نوع بار، سرعت و دما کاملا متفاوت است. روغنها و گریسها متداولترین روان کنندههایی هستند که مورد استفاده قرار میگیرند. دما بر روی ویسکوزیته تاثیر میگذارد، به همین جهت برای استفاده از بلبرینگ در دمای بالا نیاز به استفاده از روانکاری خواهید داشت که بتواند حرارت را تحمل کند. انتخاب صحیح روانکننده برای عملکرد بهتر، صرفه جویی در هزینه نگهداری و در نهایت جلوگیری از خرابی بلبرینگ ضروری است.
برخی از گریسها به طور خاص برای کار در دمای بالا طراحی و تولید شدهاند؛ اما در کنار آن امکانات دیگری دیگری نظیر مقاومت در محدوده دمای گستردهتر و توانایی عملکرد خوب در بارهای زیاد و سرعتهای بالا را نیز ارائه میدهند.
علاوه بر گریس یا روغن، روانکنندههای خشک یا روانکنندههای جامد هم میتوانند در دمای بالا مورد استفاده قرار گیرند. این مواد حتی در حالت جامد هم باعث کاهش اصطکاک بین دو سطح هستند. گرافیت یک گزینه مناسب و محبوب است؛ اما در سایر مواد از دی سولفید مولیبدن و دی سولفید تنگستن استفاده شده است. این مواد طیف وسیعی از کاربردها را در بر میگیرند؛ اما اغلب در محیطهای خلا (UUM) به دلیل کاهش خطر آلودگی استفاده میشوند. مزیت دیگری که این مواد به همراه خود دارد کاهش هزینههای نگهداری است زیرا نیاز به روانکاری مجدد نخواهند داشت.
در عصر امروزی طیف وسیعی از روانکنندهها با تحمل درجه حرارت بالا برای اهداف مختلف وجود دارد. انتخاب و استفاده صحیح از روانکنندهها یک گزینهی اختیاری نیست بلکه برای نگهداری و جلوگیری از خرابی بلبرینگ بسیار مهم است. انتخاب یک روانکار استاندارد حتی با دامنه دمایی نسبتا گسترده در کارکردهای بیش از اندازه میتواند باعث بروز مشکلاتی شود. به فرض مثال اگر بلبرینگی در دمای 1810 درجه کار میکند، شما نمیتوانید از روانکاری استفاده کنید که تا 1800 درجه حرارت را تحمل میکند.
انتخاب روانکار مناسب برای قالب
انتخاب روانکار مناسب برای قالب، یکی از مهمترین و موثرترین عوامل در انجام فرآیند فورج موفق محسوب میشود. وظیفه عمده و اصلی یک روانکار مناسب، افزایش آمار تولید، بهرهوری و نهایتا سودآوری شرکت فورج است. افزایش حداکثری عمر قالب، جلوگیری از گیرکردن و چسبیدن قطعات به قالب، کاهش قطعات مردودی، کاهش بار اعمالی برروی تجهیزات فورج و پیشگیری از شکست و یا از کارافتادگی پیش از موعد این تجهیزات تنها بخشی از مزایای استفاده از یک روانکار مناسب به شمار میآیند.
یک روانکار فورج مناسب حاوی ترکیبات شیمیایی خاص و فرمولاسیون ویژهای از این ترکیبات است تا این امکان را بدهد که فرآیند فورج مطابق با پارامترها و در محدودههای در نظر گرفته شده در صنایع فورج انجام پذیرد.
از بین سه دسته روانکار معمول در صنعت فورج که عبارتند از روانکار گرافیتی پایه روغنی، روانکار گرافیتی پایه آبی و روانکار غیر گرافیتی نوع دوم یعنی روانکار گرافیتی پایه آبی بیش از 70 درصد مصرف را در صنعت به خود اختصاص داده است. این در حالیست که استفاده از روانکارهای گرافیتی پایه روغنی هم رو به کاهش است.
ترکیب گرافیت و پودر دیسولفات مولیبدن به عنوان روانکار
گرافیت به عنوان مادهای پرکاربرد تاثیر بهسزایی در زندگی بشر دارد. طبق تحقیقات انجام شده ترکیب گرافیت و پودر دی سولفات مولیبدن (MoS2)، به علت کاهش اصطکاک در روانکاری مورد استفاده قرار میگیرند. روانکارهای خشک مانند تفلون پلی تترا فلورو اتیل (PTFE)، گرافیت و پودر دی سولفات مولیبدن (MoS2) در بیشتر پلیمرها استفاده میشوند و همهی آنها در کاهش اصطکاک و ضخامت، کاربردی هستند.
مزایای استفاده از روان کار حاوی گرافیت خالص
- روانکار حاوی گرافیت خالص در محیط هوای معمولی (نیتروژن و اکسیژن) که حاوی بخار آب نیز هستند و در دماهای بالا خوب عمل میکنند.
- روانکار حاوی گرافیت خالص در محیطهای رادیواکتیو خوب عمل میکنند.
- روانساز حاوی ۱۰ درصد MoS2 برای محیطی که هم اصطکاک بالا و هم رطوبت بالا دارد مناسبترین گزینه است.
معایب استفاده از روان کار حاوی گرافیت خالص
- روانکار حاوی گرافیت خالص برای محیطهای خلا مناسب نیستند و از به کارگیری آنها میبایست اجتناب کرد.
- روانکار حاوی گرافیت خالص دارای طول عمر کمتری نسبت به روانکاری که دارای ۵ درصد از MoS2 هست. طول عمر روانساز حاوی ۱۵ درصد MoS2 بسیار بالاتر از روانساز خالص گرافیت است.
- هرچه مقدار MoS2 بیشتر شود، قیمت آن نیز بالاتر است.
منبع: برگرفته از کتاب جامع از نفت تا گرفت؛ مسئله الکترود گرافیتی