ریشهیابی مشکل الکترود گرافیتی در کشور
ایران ۶۷ درصد از الکترود موردنیاز خود را از چین و ۱۲ درصد از هند وارد میکند. در حال حاضر واردات الکترود گرافیتی توسط ایران به دلیل آغاز مجدد تحریمها بسیار سختتر از گذشته شده است.
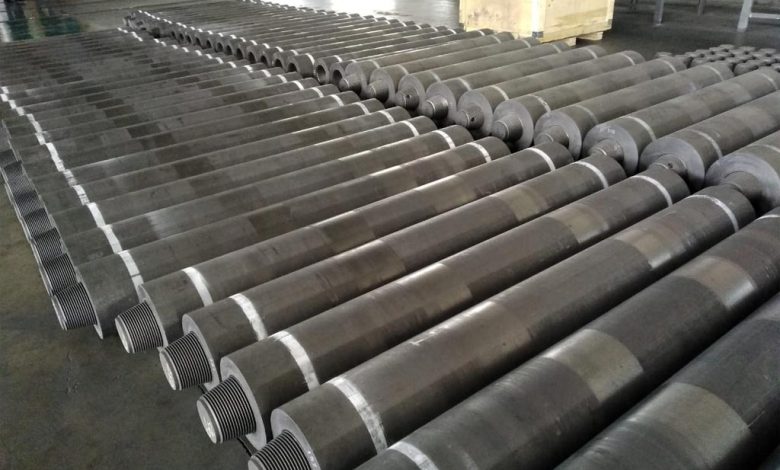
الکترود گرافیتی که کورههای قوس الکتریکی را در کارخانههای تولید فولاد میچرخاند پاشنه آشیل و اساسیترین نقطه ضعف زنجیره فولاد ایران است. تولید فولاد در کورههای قوس الکتریکی روشی است که در بیشتر کارخانههای تولیدکننده فولاد خام ایران به کار میرود.
این روش به دلیل ذخایر بالای سنگ آهن و در اختیار داشتن منابع سرشار انرژی در کشور از سوی فولادیها مورد استقبال قرار گرفته است. همچنین در روش تولید فولاد در کورههای قوس الکتریکی امکان استفاده از قراضه برای تولید وجود دارد. با این حال استفاده از این روش صنعت فولاد کشور را به کالایی اساسی و استراتژیک وابسته کرده که تاکنون امکان تولید آن در داخل فراهم نشده است، هر چند گفته شده که نخستین واحد تولید آن قرار است پس از پایان شیوع کرونا و عادی شدن شرایط به بهرهبرداری برسد.
چالش دیگری که در تولید الکترود گرافیتی وجود دارد، ماده اولیه موردنیاز آن یعنی کک سوزنی است. ذخایر کک سوزنی در سراسر جهان کمیاب و تولید آن مختص به سه کشور است که یکی از آنها آمریکاست. هر چند ژاپن و آلمان هم کک را تولید میکنند.
مشکلات الکترود گرافیتی و کک سوزنی در ایران
-
تأثیر صنعت فولادسازی چین بر تولید الکترود گرافیتی
چین از سال 1996 به عنوان بزرگترین تولیدکننده و از سال 1993 به عنوان بزرگترین مصرف کننده فولاد در دنیا مطرح بود. در حال حاضر حدود نیمی از تولید و مصرف جهانی فولاد را به خود اختصاص داده است. با توجه به آلودگیهای زیست محیطی ناشی از تولید فولاد (مخصوصا به روش کوره بلند) سیاستهای محیط زیستی در سال جاری در جهت حفظ آن به وجود آمدهاند که نتیجه آن تعطیلی 24 درصد از کل ظرفیت تولید فولادسازی در این کشور است.
طبق گزارشی درباره فولاد چین، مناطقی که دارای کورههای قوس الکتریکی القای اولیه، کوره بلندهای کوچک و تعدادی کوره بلند قدیمی بودند، بسته شدند.
در شکل زیر میزان تولیدات فولاد خام چین در سال 2016 را مشاهده میکنید.
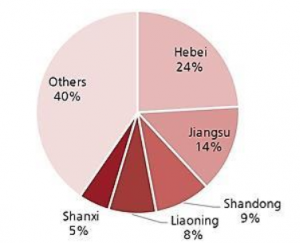
شرکت هبی با توجه به آنچه در نمودار نمایان است، بزرگترین تولیدکننده فولاد در چین است که از دو کارخانه بزرگ به اسمهای تانگشان و هاندان تشکیل شده است. تانگشان، 50 درصد از میزان تولید فولاد خود را به روش کوره بلند در 12 اكتبر 2016 کاهش داد و هاندان نیز میزان قابل توجهی را در 15 مارس 2017 کاهش داده است. این تغییر روش تولید فولاد به افزایش تقاضا برای الکترود گرافیتی منجر شده است.
-
نبود متولی صنعتی
ایمیدرو در ابتدا به عنوان متولی این صنعت شناخته میشد؛ اما در حال حاضر ایمیدرو بعد از 23 سال عدم موفقیت دیگر ادعای متولی بودن در این صنعت ندارد. هر چند این موضوع در ابتدا مثبت ارزیابی میشود، اما قطعا مصرف کنندگان هم متولی این صنعت نیستند. موضوع اینجاست که این صنعت ساخت نخست است و برای ساخت آن باید یک متولی در نظر گرفته شود. یا آن که اگر متولی از بخش خصوصی داوطلب شده است باید ترک تشریفات ساخت نخست در مورد آن رعایت شود که این موضوع هنوز محقق نشده است.
-
نبودن صنعت مشابه
فنآوریهای این صنعت به نوعی پیچیدهتر از فنآوریهای مشابه موجود در ایران است. از کک سازی تا تراشکاری هیچ فنآوری مشابه داخلی ندارد که این موضوع خطر سرمایهگذاری در حوزه فنآوری آن را به شدت افزایش میدهد.
-
متولیان گوناگون و متضاد در زنجیره تامین و مصرف
ماده اولیه تولید گرافیت نفت و محصول نهایی برای استفاده در فولاد است. این دو صنعت در طول سالهای گذشته چندان با هم همکاری نداشتهاند و گاهی منافع متضادی بین ایشان ایجاد شده است. نه شرکتهای نفتی علاقهای به استفاده از لولههای ایرانی در خطوط اکتشاف و انتقال داشتهاند و نه شرکتهای فولادی برای تولید کک نفتی خود مراجعهای به پالایشگاهها داشتهاند. این دو صنعت به علت اینکه سابقه همکاری با هم نداشتهاند به سختی میتوانند قراردادهای بلند مدت تامین و مصرف مواد زنجیره را منعقد سازند.
-
شکست مدعیان دانشبنیان
متاسفانه در چند سال گذشته افراد زیادی ادعا کردهاند که الکترود گرافیتی یا ککسوزنی تولید میکنند و از آنجا که بنیانهای علمی این ادعاها کم بوده است. به نوعی یک باور به ناتوانی در میان مدیران و کارشناسان کشور ایجاد شده و احساس میشود شرکتهای دانشبنیان ایرانی توان فعالیت در این عرصه را ندارند. اشکال در افراط و تفریط نسبت به جایگاه شرکتهای دانشبنیان باعث شده به نوعی در این حوزه ناامیدی به وجود آید.
-
صادر کنندگان قیر
مشکلاتی که در موضوع واردکنندگان الکترود اشاره شد در خصوص صادرکنندگان قیر هم وجود دارد. صادرات قیر برای پالایشگاهها جذاب است و افراد زیادی در این زیستبوم فعالیت میکنند. سالانه چند میلیون تن قیر و برشهای سنگین نفتی صادر میشود که در صورت تاسیس واحد کک سازی تاخیری این قیرها به مصارف داخلی خواهند رسید. در نتیجه نسبت به تاسیس این واحدها مقاومتهایی وجود دارد.
-
عدم ضمانت خرید
فولاد سازها نسبت به شرکتهای ایرانی سختگیرتر از شرکتهای خارجی هستند. در حالی که هنوز هیچ سنجهای در خصوص کالاهای خریداری شده در ایران انجام نمیشود؛ اما برای تامین الکترود هیچگونه ضمانت خریدی صادر نمیشود. در نتیجه خطر سرمایهگذاری در بخش بازاریابی برای سرمایهگذاران افزایش خواهد یافت.
-
نیاز ایران به الکترود گرافیتی
تولید فولاد ایران در سال 1396، 5/21 میلیون تن بود. همه فولادسازیها به جز ذوب آهن اصفهان از روش کوره قوس الکتریکی استفاده میکنند. میزان تولید ذوب آهن 8/2 میلیون تن در سال است. درنتیجه 7/18 میلیون تن فولاد به روش کوره قوس الکتریکی تولید میشوند. میانگین مصرف الکترودگرافیتی در یک تن فولاد 3 کیلوگرم در ایران است. واردات الکترود گرافیتی مورد نیاز در ایران بیشتر از چین و هند انجام میشود.
به طور مثال ایران در سال 1396، 67227 تن الکترود از چین و 11787 تن از هند الکترود گرافیتی وارد کرده است. همچنین بر اساس افق 1404 تولید فولاد کشور باید به 55 میلیون تن برسد که براساس چشمانداز به بیش از 100 هزار تن الکترود نیاز خواهیم داشت.
مشکلات واردات الکترود گرافیتی به ایران
بنا به گزارش استیل مینت 440 میلیون دلار ارز 4200 تومانی در اختیار فولادسازان قرار گرفته است؛ اما اين رقم كافی نيست. اگر میانگین قیمت هر تن الکترود گرافیتی را 15000 دلار در نظر بگیریم صرفا میتوان به طور تقریبی 30000 تن الکترود یعنی میزان مصرف 4 ماه فولادسازها را تأمین کرد.
همچنین تولیدکننده اصلی الکترود هندی (گرافیت ایندیا) که معامله با ایران 6 تا 7 درصد درآمدش را در برمیگیرد اظهار کرده باید ریسکهای احتمالی ناشی از تحریمهای آمریکا را بررسی کند، با این حال امیدوار است این سیاستها از بازار نفت به بازار سایر کالاهای صنعتی ازجمله الکترود گرافیتی کشانده نشود. در هر حال این شرکت با ایران قرارداد تأمین دارد که باید تا سپتامبر 2018 الکترود مورد نیاز ایران را تأمین کند. به این معنا که تحریمهای آمریکا فعلا اثر چندانی بر صنعت فولاد ایران نخواهد داشت. البته الکترود گرافیتی جز اولویتهای تحریمی دولت آمریکا در آبان ماه 1397 است که این امر موجب ایجاد مخاطره در تأمین الکترودگرافیتی خواهد شد.
کک سوزنی در ایران
با توجه به اینکه ککسوزنی خوراک اولیه برای ساخت الکترود گرافیتی است، تأمین آن گلوگاه تولید الکترود گرافیتی در داخل کشور است.برای رفع این نیاز لازم است تا این ماده وارد شود و یا در داخل تولید شود که واردات آن با مشکلات زیر مواجه است:
۱. کک سوزنی علاوه بر الکترود گرافیتی و باتری لیتیومی در صنایع هستهای نیز استفاده دارد در نتیجه به دلیل اعمال تحریمها واردات آن بسیار سخت میشود.
۲. با توجه به اینکه میزان تقاضا برای کک سوزنی از عرضه آن بیشتر است در نتیجه فراهم کردن آن دشوار است.
۳. با توجه به افزایش قیمت کک سوزنی و قیمت بالای دلار در ایران این عمل هزینه بسیار زیادی خواهد داشت.
هماکنون فولادسازیها و بسیاری از فعالان دیگر در این زمینه مشغول به فعالیت هستند؛ اما تاکنون کک سوزنی در داخل کشور به صورت صنعتی ساخته نشده است و تا وقتی که تمام زنجیره ساخت الکترود گرافیتی از تصفیه نفت گرفته تا تراشکاری الکترودها در ایران شکل نگیرد وابستگی به الکترود همچنان برقرار خواهد بود.
به همین دلیل حل مساله به سادگی ساخت یک کارخانه نیست. بیشترین زمان ساخت مربوط به واحدهای کک سازی است و در نتیجه حتی اگر سرمایه کل زنجیره تامین شود برای ساخت یک صنعت مستقل به حداقل پنج سال زمان نیاز خواهد بود.
وضعیت تولید الکترود گرافیتی در جهان
ظرفیت تولید الکترود گرافیتی در جهان تقریبا دو میلیون تن در سال است و عموم تولیدکنندگان این محصول در کشورهایی از جمله آمریکا، آلمان، چین، ژاپن و هند قرار دارند.
در شکل زیر میزان تولید الکترود گرافیتی در سالهای مختلف نشان داده شده است. شکل بعد نیز شرکتهای پیشرو در زمینه تولید الکترود گرافیتی در سال 2017 را نشان میدهد که شرکت Showa Denko با تولید 289 هزار تن تولید سالانه در صدر این فهرست قرار دارد.
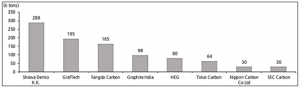
منبع:برگرفته از کتاب جامع از نفت تا گرفت؛ مسئله الکترود گرافیتی