بررسی نقش کلسیناسیون در کک نفتی
کک نفتی معمولا از باقیماندهی مواد حاصل از کرکینگ و فرآیند تقطیر نفت در پالایشگاهها حاصل میشود. این مواد باقیمانده طی فرآیندی (در کورههای حرارتی) با حرارت بیشتر و خردایش در کوره تبدیل به کک کلسینه میشود.
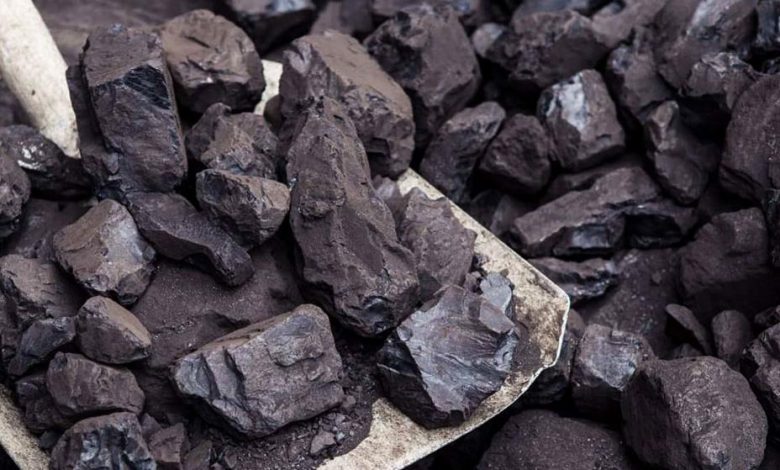
فرآیند تولید مواد اولیه کربندار با عملیات حرارتی در دمای بالا برای تخلیه رطوبت و مواد فرار موجود در آن و به موجب آن بهبود خصوصیات فیزیکی و شیمیایی مواد اولیه را کلسینه کردن میگویند. به طور کلی، مواد اولیه کربندار با گاز و مواد فرار خود به عنوان منبع گرما کلسینه میشوند و بالاترین دما 1250 تا 1350 درجه سانتی گراد است. کلسیناسیون باعث تغییرات عمیقی در ساختار و خصوصیات فیزیکی و شیمیایی مواد اولیه کربنی میشود که عمدتا در بهبود چگالی کک، مقاومت مکانیکی، هدایت، بهبود پایداری شیمیایی کک و خواص آنتی اکسیدانی موثر است و پایه و اساس فرآیند بعدی را ایجاد میکند.
فرآیند کلسینه شدن شامل: خشک کردن رطوبت درون کک که به دنبال تخریب هیدروکربنهای باقیمانده در کک خام صورت میپذیرد و در نهایت کک کوچک و بسیار متراکم تولید میشود. در این صورت کک خصوصیات الکتریکی مطلوب که مناسب برای تولید آند و الکترود است را به دست میآورد.
روشهای کلسیناسیون
دو روش برای کلسیناسیون کک وجود دارد: rotary-kilnو .rotary-heart روش rotary-kiln یا کوره دوار روشی قدیمیتر و rotary-heart یا کوره دوار حرارتی روشی نوینتر است. دو روش از نظر مفهوم یکسان؛ اما از نظر مکانیکی متفاوت هستند. ککی که مواد فرار و رطوبت آن حذف نشده باشد، به کک سبز معروف است. کک سبز بعد از تخلیه به سنگ شکن و در ادامه بهkiln (یک نوعی کوره حرارتی عایق که برای تکمیل فرآیند گرمای لازم را تولید میکند) میرود. در kiln کک بر خلاف جهت جریان حرارتی حرکت میكند. حرارت فرآیندی توسط یک مشعل تأمین میشود. سوختن مواد فرار در کک سبز نیز منبع دیگر این جریان حرارتی است. بعد از، kiln مواد به کولر دوار منتقل و در آنجا با آب مستقیم اسپری شده خنک میشوند. سپس با جریان هوا خنک شده و در ادامه به مخزن منتقل میشوند.
کوره دوار ( Rotary kiln )
کوره دوار، یک سیلندر طولانی و دوار افقی با پوشش داخلی نسوز است. کک از یک انتها وارد شده و در میان کوره به انتهای دیگر منتقل میشود. کوره به طرف پایین و در محل انتهای تخلیه زاویه دار است که به حرکت و جابجایی کک کمک میکند. سوخت و هوا به داخل کوره در موقعیتهای مختلفی تزریق میشود که موجب رهاسازی مواد فرار در کک میگردد. کک به داخل کوره منتقل شده و در اثر تماس با گازهای داغ که در جهت عکس جریان کک حرکت دارد، باعث سهولت در انتقال حرارت به ذرات کک میشود. همچنین به شکسته شدن کک به قطعات کوچکتر کمک میکند ولی با تولید گرد و خاک بیشتری تولید و یا سوختن داخل کوره به سمت گازهای خروجی هدایت میشوند که نهایتا در قسمت دیگری (که پس از حرارت نامیده میشود) میسوزد.
کوره دوار حرارتی ( Rotary hearth )
دستگاه کوره دوار حرارتی که برای کلسینه کردن است، صفحهی دوار چرخشی صافی با پوشش نسوز و دارای سقفی در بالای آن برای محدود کردن گازها به شمار میرود. قطر کوره در مقیاس تجاری معادل 10-28 متر است.کک از محفظه خوراک وارد محفظهی دیگری به نام شوتینگ برای انتقال به داخل کوره که پیرامون آن حرارت جریان دارد، منتقل میشود. این کک در یک مسیر مارپیچی به حرکتش ادامه میدهد تا زمانیکه در مرکز داخلی محفظه چرخنده که همانند گودال خیس است، تخلیه شود.
کک در هر یک از چرخشهای کوره، زیر و رو میشود و آن را به مسیر جریانهای بعدی منتقل میکند. این عمل چرخشی، مواد را با هم مخلوط و جابجا میکند و آن را در معرض سطح خنک کننده جدید قرار میدهد تا گرمای آن را جذب کند. کل زمان فرآیند داخلی کوره بستگی به نوع متریال و گریدی که میخواهد تولید شود، دارد؛ اما معمولا 1 ساعت زمان میبرد. کک در مخزن مرطوب نگهداری شده و برای تولید کک کلسینه حدود 15 تا 20 دقیقه در مجاورت حرارت میماند باید از تبادل حرارتی آن قبل از تخلیه به داخل درام مطمئن شد. افزایش کک از طریق شوت خوراک باعث افزایش عمق ضخامت سطح کوره میشود و کاهش ورود کک به شوت خوراک باعث کاهش عمق سطح کوره میشود.
کک داخل کوره تقریبا 50 میلی متر پایینتر از ارتفاع فعال سطح (بستر) قرار میگیرد که برای محافظت و جلوگیری از سایش عایق نسوز است. در داخل محفظه کوره دوار حرارتی بخش عمدهی مواد فرار کک در اثر حرارت آزاد میشود. این مواد فرار با شروع فرآیند هوادهی در پیرامون محفظه و از طریق سقف کوره خارج میشوند. با توجه به محتوای مواد فرار و رطوبت در کک فرآیند هوادهی ممکن است. باید از قبل گرما ایجاد و حرارت مورد نیاز کوره از قبل تامین شده باشد. در بسیاری از موارد سوخت کمکی دیگری برای عملکرد کوره مورد نیاز نیست که بتواند انرژی مطلوب را ایجاد کند.
اگر میزان مواد فرار در ماده اولیه کک نسبتا بالا و میزان رطوبت آن پایین باشد، کوره ممکن است در درجه حرارت زیر حد نرمال کار کند. این موضوع باعث میشود بخشی از مواد فرار آزاد نشده و از بالا رفتن درجه حرارت در کوره جلوگیری میکند. مواد فرار باقیمانده در داخل دودکش، از طریق ورود هوا جذب و میسوزند. در دودکش خروجی، سطح اکسیژن کنترل و پایش میشود تا از حذف کامل (سوختن) کلیه مواد فرار قبل از اینکه گازهای اضافی وارد سیستم بازیابی حرارتی شود، اطمینان حاصل کنند.
کک کلسینه در داخل کوره خورد میشود (شخم زده میشود) و به طرف گودال خیس که در مرکز کوره قرار دارد میرود. داخل این گودال خیس متصل به بخش چرخش کوره بوده و در چرخش است. کک در این گودال حدود 15-20 دقیقه میماند که مطمئن شوند تمام کک در حرارت پایدار است. این کار باعث میشود که تمام کک خصوصیات یکنواخت داشته باشد. این یک فاکتور مهمی در تولید آند با کیفیت بالا است. در انتهای گودال خیس میز تخلیه چرخشی کوچکی وجود دارد که قطر آن بین 3-5 متر بوده و یک فن نسوز با سپر محافظ گرد و خاک که با سیستم خنک کننده توسط آب به آن متصل است. این قسمت مکانیزمی دارد که میتواند خرد شدن (شخم زدن) کک داخل شوت را به طرف سیستم خنک کننده آبی را کنترل کند. سرعت چرخش میز تخلیه به صورت مستقل کنترل شده و باعث میشود سطح گودال خیس هم به کنترل درآید و ارتفاع کافی خودش را داشته باشد. این موضوع باعث جلوگیری از تجمع ناخالصی در محوطه کلسینه شدن میشود.
نقش کلسینه شدن در کک سازی
کک نفتی یک محصول فرعی حاصل از پالایش نفت خام که ماده اصلی تشکیل دهنده آن کربن است، مقدار زیادی گوگرد و فلزات سنگین مانند نیکل و وانادیم دارد. کک نفتی کلسینه شده از طریق انجام عملیات کلسینه کردن بر روی کک خام به دست میآید. طی این فرایند، بخشی از مواد فرار و رطوبت موجود در کک خام از ماده خارج شده و در نتیجه درصد وزنی کربن افزایش مییابد.کک نفتی کلسینه شده در صنایع آلومینیوم، آند سازی، صنایع فولاد، صنایع ریختهگری، حفاظت کاتدی و… کاربرد فراوان دارد.
منابع:
برگرفته از کتاب جامع از نفت تا گرفت؛ مسئله الکترود گرافیتی
https://www.exirfaraz.com/blog-content/7