الزام شکست تابوی عدم تابوی دستیابی به کک سوزنی در کشور
با توجه به اینکه کک سوزنی خوراک اولیه برای ساخت الکترود گرافیتی است، تأمین آن گلوگاه تولید الکترود گرافیتی در داخل کشور به شمار میرود. برای رفع این نیاز باید ماده مذکور وارد و یا در داخل تولید شود. در حال حاضر واردات آن با مشکلاتی مواجه است.
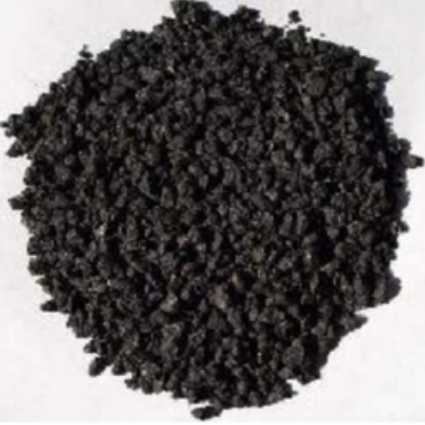
تا زمانی که تمام زنجیره ساخت الکترود گرافیتی از تصفیه نفت گرفته تا تراشکاری الکترودها در کشورمان انجام نشود، وابستگی به واردات الکترود همچنان برقرار است. به همین دلیل حل مساله دست یابی به دانش ساخت الکترود گرافیتی به سادگی ساخت یک کارخانه نیست. بیشترین زمان ساخت مربوط به واحدهای کک سازی است. در نتیجه حتی اگر سرمایه کل زنجیره تامین شود برای ساخت یک صنعت مستقل حداقل به پنج سال زمان نیاز است.
همچنین، فناوریهای این صنعت به نوعی پیچیدهتر از فناوریهای مشابه و موجود در کشور است. از کک سازی تا تراشکاری هیچ فناوری مشابه داخلی ندارد. این موضوع خطر سرمایهگذاری در حوزه فناوری آن را به شدت افزایش میدهد.
دلایل عدم دستیابی به این صنعت در کشور
تولیدکنندگان گرافیت در کشور به موضوع تحریمها اشراف دارند. تحریمکنندگان از اینکه فناوری ساخت گرافیت در ایران راهاندازی شود واهمه داشته و این ترس خود را با تهدید و ارعاب سرمایهگذاران برای ورود به این بخش نشان دادهاند. به نوعی تحریم و تهدید خارجی که نسبت به نهادهای داخلی مطرح میشود در همین راستا خواهد بود. در چند سال گذشته چندین شرکت متعدد به علت فعالیت در حوزه گرافیت تحریم شدهاند، به همین دلیل خطر سرمایهگذاری در این صنعت افزایش یافته است.
ماده اولیه تولید گرافیت نفت و محصول نهایی برای استفاده در فولاد است. این دو صنعت سالهای گذشته چندان با هم همکاری نداشتهاند و گاهی منافع متضادی میان آنها ایجاد شده است. نه شرکتهای نفتی علاقهای به استفاده از لولههای ایرانی در خطوط اکتشاف و انتقال داشتهاند و نه شرکتهای فولادی برای تولید کک نفتی خود مراجعهای به پالایشگاهها داشتهاند. عدم همکاری بین این دو صنعت باعث میشود به سختی قراردادهای بلند مدت تامین و مصرف مواد زنجیره را منعقد سازند.
متاسفانه در چند سال گذشته افراد زیادی ادعا کردهاند که الکترود گرافیتی یا کک سوزنی تولید میکنند. از آنجایی که بنیانهای علمی این ادعاها کم بود، نوعی یک باور به ناتوانی در میان مدیران و کارشناسان کشور ایجاد شد و احساس میشود شرکتهای دانش بنیان ایرانی توان فعالیت در این عرصه را ندارند. اشکال در افراط و تفریط نسبت به جایگاه شرکتهای دانش بنیان باعث شده، نوعی ناامیدی در حوزه به وجود آید.
مشکلات اشاره شده در موضوع وارد کنندگان الکترود، در خصوص صادر کنندگان قیر هم وجود دارد. صادرات قیر برای پالایشگاهها جذاب است و افراد زیادی در این زیست بوم فعالیت میکنند. سالانه چند میلیون تن قیر و برشهای سنگین نفتی صادر میشود. در صورت تاسیس واحد کک سازی تاخیری این قیرها به مصارف داخلی میرسند. در نتیجه نسبت به تاسیس این واحدها مقاومتهایی وجود دارد.
فولاد سازها نسبت به شرکتهای ایرانی سختگیرتر از شرکتهای خارجی هستند. در حالی که هنوز هیچ سنجهای در خصوص کالاهای خریداری شده در ایران انجام نمیشود همچنین برای تامین الکترود هیچگونه ضمانت خریدی صادر نمیشود. در نتیجه خطر سرمایهگذاری برای سرمایهگذاران افزایش خواهد یافت.
در سالهای گذشته و با ورود چالشهای مذکور به دانشگاهها تعدادی از اساتید وارد حوزه فعالیت شدند؛ اما این چالشها به علت نبود حمایت از صنایع و تا حدودی غیر کاربردی بودن آنها ادامه نیافت. ادامه این چالشها میتواند حساسیت دانشگاهیان و شرکتهای دانش بنیان را به این موضوع تقویت کند.
پالایشگاهها و پتروشیمیها هر دو امکان تولید کک اسفنجی و سوزنی را دارند؛ اما هیچکدام تاکنون علاقه و تمایلی به این کار نشان ندادهاند. به این دلیل که مازوت پر گوگرد به عنوان سوخت کشتی یا خوراک کارخانههای دودهسازی قابل استفاده است.
یکی دیگر از مشکلات پالایشگاهها و پتروشیمیها این است که باید برای ورود میعانات سبک واحد کک سازی برنامه ریزی فنی لازم را انجام دهند. درحالیکه پتروشیمیها دانش اولیه برای این کار را ندارند. همچنین برشهای سنگین پالایشگاهها و پروشیمیها به اندازه کافی برای تولید کک مرغوب مناسب نیست و باید فرایندهایی مانند کاهش گوگرد و سایر موارد را انجام دهند. این موضوع درگیریهای فنی زیادی دارد.
راهکارهای موجود برای حل این مسئله
از بین بردن تفکرات اشتباهی مانند: دانش فنی تولید الکترود گرافیتی پیچیده است و ایران قادر به دستیابی به آن نیست، مواد اولیه تولید الکترود گرافیتی کک سوزنی است که دانش تولید آن در انحصار آمریکا و ژاپن است و مواد اولیه کک سوزنی کک نفتی است که در ایران قابل تامین نیست، میتواند راه را برای نیل به این هدف هموارتر کند.
هر چند کک سوزنی یکی از مشکلات در راهاندازی این صنعت است؛ اما در صورتی که بتوان آن را حتی در مقیاس نیمه صنعتی و یا آزمایشگاهی در کشور تولید کرد، میتواند انگیزه خوبی به سرمایهگذاران برای تولید الکترود گرافیتی بدهد.
نرخ بازگشت سرمایه برای واحدهای گرافیت سازی در شرکتهای فولاد سازی بسیار مناسب است. پس فولادسازها به راحتی میتوانند نسبت به ساخت یک کارگاه در کارخانه خود اقدام کنند. با توجه به وجود نیتروژن اضافه در کارخانجات فولاد میتوان کارگاههای گرافیتسازی را با روش خنکسازی سریع با نیتروژن ترکیب کرد که این کار منجر به افزایش ظرفیت کارگاههای گرافیتسازی خواهد شد. استفاده از نیتروژن مازاد در کارخانجات فولاد سازی، میتوان با ظرفیتی تقریبا دو برابر ظرفیت معمولی نسبت به گرافیت سازی اقدام کرد.
تشویق فولاد سازها به ساخت خط گرافیتسازی میتواند در قالب مشوقهای مالیاتی یا وام باشد؛ اما به هرحال ساخت این خطوط توسط فولاد سازها از زوایای داشتن برق، داشتن نیتروژن اضافه و به دنبال آن بهرهبرداری ساده و حاشیه سود مناسب قابل توجه است.
دو شرکت پالایش قطران اصفهان و زرند به منظور تولید فرآوردههای حاصل از زغال سنگ ساخته شدهاند. درحال حاضر شرکت پالایش قطران اصفهان 100 هزار تن در سال تولید دارد؛ اما بیشتر حجم تولید آن دارای مشتری است و مقدار کمی قابلیت خرید دارد. در صورتی که حدود 3 تا 5 هزار تن کک سوزنی میتوان تولید کرد. شرکت قطران زرند به دلیل اینکه زغال سنگ مطلوب ندارد، تعطیل است. این شرکت که برای هلدینگ میدکو است دارای تجهیزات و امکانات زیادی است که برای تولید کک میتوان از ظرفیت این واحد استفاده کرد.
لازم به ذکر است گروه دانش بنیان پاترون با توجه به بحران الکترود گرافیتی و با تکیه بر دانش فنی خود در راستای کاهش ضریب مصرف الکترود برای اولین بار در کشور اقدام به تولید پوششی با نام تجاری الکوپات کرده است. این پوشش از اکسیداسیون جداره الکترود گرافیتی، با توجه به شرایط اپراتوری هر کارخانه، جلوگیری میکند و به موجب آن کاهش ضریب مصرف الکترود را حدودا از ۱۰ تا ۲۰ درصد در بر خواهد داشت. الکوپات هم اکنون در بزرگترین کارخانه فولادسازی خاورمیانه (فولاد مبارکه اصفهان)، فولاد هرمزگان، فولاد کاوه جنوب کیش و فولاد سازان دیگر مورد استفاده قرار میگیرد. همچنین کاهش مصرف الکترود گرافیتی با الکوپات به تایید دیگر فولاد سازان منطقه هم رسیده است.
راهکارهای این چنینی و تعریف پروژههای کاهش مصرف الکترود گرافیتی میتواند بخشی از مشکلات فولاد سازان کشور را در راستای تامین الکترود گرافیتی کم کند. لازم به ذکر است میانگین ضریب مصرف الکترود گرافیتی در جهان، حتی با فرض مصرف آهن اسفنجی، زیر ۲ کیلوگرم به ازای هرتن فولاد است در حالی که در کشورمان میانگین مصرف آن، بالای ۲ کیلوگرم فولاد است. امید است، با توجه به بحران الکترود و وضعیت تحریم ها، با استفاده از الکوپات و پروژههای کاهش مصرف الکترود گرافیتی، با کنترل فرآیند خنک سازی و تنظیم الکترود و …، بتوانیم رکورددار کاهش مصرف الکترود گرافیتی در جهان باشیم.
برگرفته از کتاب جامع از نفت تا گرفت؛ مسئله الکترود گرافیتی
منابع:
- https://www.ahanpakhsh.com/news/metal-news
- https://meyarco.ir/reports