چالش خودکفایی در الکترودگرافیتی
تولید الکترود گرافیتی در کشور با چالشهایی رو به رو است که هنوز به طور کامل رفع نشده و ایران به خودکفایی نرسیده است.
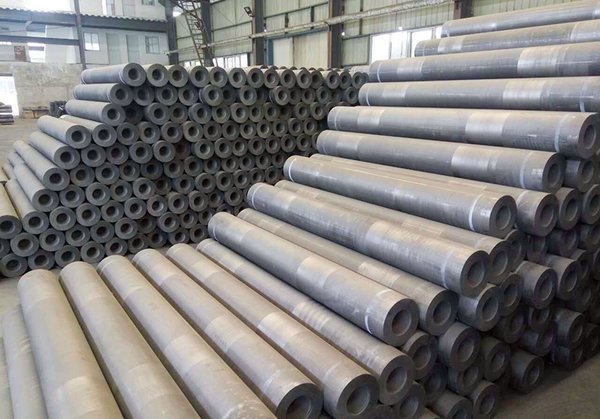
کاربرد الکترود گرافیتی در کورههای القایی است. درحال حاضر به دلیل آلایندگی کمتر کورههای القایی و مصرف سوخت پاک الکتریکی این کورهها کاربرد بیشتری دارند که کاهش مصرف انرژی، عدم استفاده از سوخت های فسیلی، هزینه تمام شده پایینتر تولید نسبت به کورههای فسیلی از عوامل گسترش کورههای القایی بوده که الکترودگرافیتی جز اصلی این کورهها هستند.
الکترودگرافیتی نقش موثری در کیفیت مذاب تولیدی درون کورهها داشته و با توجه به عدم نیاز به در دسترس بودن تکنولوژی بالا در تولید ساخت آن نسبتا ساده است. الکترود گرافیتی از مواد اساسی در فرآیند تولید و ذوب فلزات بوده و از مهمترین اجزای کورههای قوس الکتریکی است. در حال حاضر در کشور بیش از هشتاد درصد تولید فولاد به روش احیای مستقیم و کورههای ذوب الکتریکی صورت میگیرد؛ بنابراین تولیدکنندگان فولاد در کشور و جهان نگاه ویژهای به این محصول دارند چرا که الکترود گرافیتی مصرفی بوده و پس از استفاده در زمان مشخصی در کوره نیاز به تعویض دارد.
مواد اولیه مورد نیاز برای تولید الکترودگرافیتی، کک سوزنی است که تولید با کیفیت بالای این محصول در انحصار کشورهای معدودی است؛ از این رو برای بومی سازی الکترودگرافیتی، دستیابی به تولید کک سوزنی، اهمیت بالایی دارد که شرکت فولاد مبارکه در راستای بومی سازی آن قدم برداشته است. پیش از این معاونت علمی و فناوری ریاست جمهوری به منظور بومی سازی و توسعه دانش فنی و فرآیند تولید کک سوزنی و فرآوری خوراک آن فراخوانی با محورهای گوگرد از قیر قطران زغال سنگ، فرایند تولید کک اسفنجی و کک سوزنی، و تولید QI زدایی از روغنهای آروماتیکی سنگین، جداسازی ذرات کک سوزنی با استفاده از خوراکهایی که نیاز به کاهش گوگرد و ذرات جامد ندارند را انجام داده است.
فولاد مبارکه، در پروژه کنسانترهسازی سنگان مشارکت دارد و استراتژی که از ابتدای سال 98 برای خود تعریف کرده و حمایتهایی در افزایش تولید داشته است، تا جایی که علاوه بر افزایش ظرفیت واحدهای قدیمی، در راهاندازی بزرگترین پروژه کنسانترهسازی کشور به ظرفیت 5 میلیون تن حداکثر اقدام لازم را به کار گیرد تا زودتر وارد فرایند تولید شود. پیش از این شرکت فولاد مبارکه در سال 96 واحد گندله سازی را با سرمایهگذاری هزار میلیارد تومان محقق کرد که برای اجرای آن 200 میلیارد تومان در حوزه زیرساختهای آن نیز سرمایهگذاری کرده است.
تولید الکترودگرافیتی در ایران
توليد فولاد به روش كوره قوس الكتريكي شديدا به الكترود گرافيتي وابسته است و هنوز هم هيچ جايگزيني براي آن وجود ندارد. با توجه به اهميت استراتژيك اين كالا فعاليتها براي ايجاد كارخانه الكترودگرافيتي در كشور از دهه 70 شمسي شروع شد.
از آنجایی كه توليد الكترود گرافيتي به شدت به كك سوزني وابسته است كه توليد آن در انحصار چند كشور است. فعاليت براي ايجاد كارخانه پتروليوم کک و توليد کک سوزني حدودا از دهه 90 شمسي آغاز شد. در حال حاضر دستيابي به توليد و تكنولوژي توليد كك سوزني انحصارتر و به مراتب سختتر از دسترسي به توليد الكترود گرافيتي است. گرچه رفتن بسوي توليد الكترود گرافيتي و پتروليوم كك و كك سوزني به عنوان ماده اوليه توليد الكترود گرافيتي را با دههها تاخير شروع كرديم ولي اخيرا خبرهاي خوشي در اين خصوص هست كه يكي از شركتهاي دانش بنيان كشور توانسته است به توانمندي توليد كك سوزني در مقياس آزمايشگاهي دست يابد و با چند شركت بزرگ تفاهم نامهاي براي توليد نيمه صنعتي آن امضا کند.
چالش تولید الکترود در ایران
الکترودگرافیتی که کورههای قوس الکتریکی را در کارخانههای تولید فولاد میچرخاند پاشنه آشیل و اساسیترین نقطه ضعف زنجیره فولاد ایران است. تولید فولاد در کورههای قوس الکتریکی روشی است که در بیشتر کارخانههای تولیدکننده فولاد خام ایران به کار میرود. این روش به دلیل ذخایر بالای سنگ آهن و در اختیار داشتن منابع سرشار انرژی در کشور از سوی فولادیها مورد استقبال قرار گرفته است.
همچنین در روش تولید فولاد در کورههای قوس الکتریکی امکان استفاده از قراضه برای تولید وجود دارد. با این حال استفاده از این روش صنعت فولاد کشور را به کالایی اساسی و استراتژیک وابسته کرده که تاکنون امکان تولید آن در داخل فراهم نشده است، هر چند گفته شده که نخستین واحد تولید آن قرار است پس از پایان شیوع کرونا و عادی شدن شرایط به بهرهبرداری برسد.
چالش دیگری که در تولید الکترودگرافیتی وجود دارد، ماده اولیه موردنیاز آن، کک سوزنی است. ذخایر کک سوزنی در سراسر جهان کمیاب و تولید آن مختص به سه کشور است که یکی از آنها آمریکاست هر چند ژاپن و آلمان هم کک را تولید میکنند.
در سالهای 96 و 97 بود که الکترودگرافیتی تبدیل به مشکلی بزرگ برای فولادسازان شد. آن روزها گذشت و شرکتهایی مانند فولاد مبارکه و ذوب آهن که بیشترین نیاز را به این محصول دارند، با پیگیری معاون وقت وزیر صنعت، معدن و تجارت در امر واردات چالش را پشت سر گذاشتند؛ اما سایه این ضعف همچنان بر سر صنعت فولاد ایران برقرار است.
به نظر میرسد آنچه باعث شده این ضعف تا به الان از صنعت فولاد ایران برطرف نشود، ارزانتر بودن واردات از تولید است. مبدا بیشترین الکترودگرافیتی وارداتی به ایران چین است که هر چند شریک تجاری خوبی برای ایران در سالهای تحریم بوده، اما در نهایت این اتفاق به وابستگی کشور انجامیده است.
منبع: http://www.eghtesadebazar.ir
https://matsa.co/product
http://www.niscoir.com/Portal/home/?publishing