کک نفتی و تولید فولاد
با توجه به استراتژیک بودن تأمین الکترود کوره قوس در صنایع فولادسازی داخل کشور، بومیسازی ساخت الکترود به عنوان یکی از طرحهای ویژه جهت توسعه تولید فولاد کشور مدنظر قرار گرفته است.
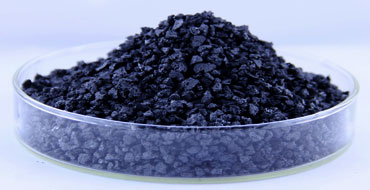
با توجه به استراتژیک بودن تأمین الکترود کوره قوس در صنایع فولادسازی داخل کشور، بومیسازی ساخت الکترود به عنوان یکی از طرحهای ویژه جهت توسعه تولید فولاد کشور مدنظر قرار گرفته است. ماده اولیه اصلی الکترود گرافیتی، کک سوزنی (نیدل کک) است که از سنتز پسماندهای سنگین نفتی یا محصولات جانبی حاصل از تولید کک متالورژی با مشخصات کیفی موردنظر و به روش ککسازی تأخیری تولید میشود. از جمله شاخصهای اصلی کیفی این کک میتوان به گوگرد کمتر از ۰.۵ درصد وزنی، شاخص بافت نوری (OTI) حدود ۳۰ و ضریب انبساط حرارتی (CTE) کمتر از ℃/۱ (-۷)۱۰ اشاره کرد.
ککسوزنی از پسماندهای سنگین نفتی طی فرایند ککسازی تأخیری و پس از آن فرایند کلسیناسیون توسط کوره دوار تولید میشود. از جمله مهمترین شاخصهای کیفی پسماند نفتی مورد نیاز شامل گوگرد کمتر از یک درصد وزنی، خاکستر کمتر از ۰.۳ درصد وزنی و درجه آروماتیکی حدود ۶۵ درصد وزنی با کربن کنرادسون (CCR) بین ۸ الی ۱۰ درصد وزنی است.
کاربرد کک سوزنی در ساخت الکترودهای گرافیتی
کورههای قوس الکتریکی از سه جزء اصلی بدنه، سقف و الکترود گرافیتی تشکیل شده است. این کورهها عمدتاً به دو سامانه برجسته جریان متناوب (AC) و جریان مستقیم (DC) تقسیمبندی میشوند. در کورههای جریان متناوب، سه الکترود گرافیتی داخل کوره قرار میگیرد و در جریان مستقیم تنها از یک الکترود استفاده میشود که وظیفه هدایت جریان الکتریکی را به عهده دارند. در جدول ۱ مشخصات کاری کوره قوس از نوع AC مشخص شده است:
جدول ۱- مشخصات فنی کوره قوس AC
مشخصه | واحد | مقدار |
قطر کوره | m | 6-8 |
جریان | kA | 50-70 |
ولتاژ | V | 600-1500 |
دمای ذوب | 1620-1680 | |
زمان | min | 50-80 |
زمان پاور | min | 42-75 |
انرژی الکتریکی مصرفی | k | 350-550 |
مقدار کل مصرف انرژی | K | 600-700 |
مصرف االکترود | 2.1-8.2 |
کار الکترود انتقال جریان از الکترود به سمت بار کوره و تولید حرارت از طریق ایجاد قوس الکتریکی است. این الکترودها که در حین کار در کوره در اثر اکسیداسیون، تصعید و شکستگی از بین میروند، یک ماده مصرفی برای صنایع فولادسازی محسوب میشوند. به طوری که میزان مصرف آن برای تهیه هر تن فولاد بین یک الی ۳ کیلوگرم است.
این دامنه زیاد در مقدار مصرف الکترود علاوه بر اینکه به شرایط عملیاتی و تناژ کوره وابسته است، به کیفیت الکترود نیز بستگی دارد. همچنین به طور تجربی در صنایع فولادسازی برآوردشده است که در هر بار ذوبگیری معمولا بین ۳۰۰ الی ۵۰۰ میلیمتر از طول نوک الکترود کاسته میشود. بنابراین، این الکترودها که دارای طول ۱.۵ الی ۲.۵ متر و قطرهای متفاوت (بسته به تناژکوره) هستند به طور خوردکار با هر بار ذوبگیری به سمت پایین حرکت میکنند، تا فاصله بین نوک الکترود تا سطح شارژ ثابت باقی بماند.
عبور جریان الکتریکی و دمای کاری بسیار بالا در الکترود، تکنولوژی ساخت این قطعات را در جایگاه ویژهای قرار میدهد. در شکل ۱ روند تولید الکترود گرافیتی نشان داده شدهاست:
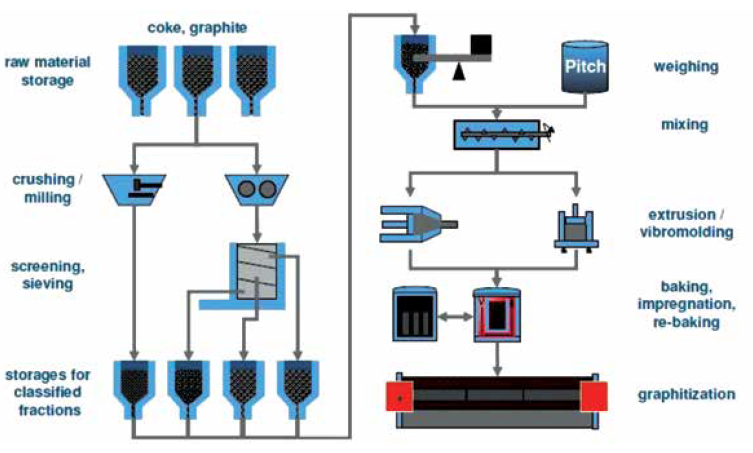
شکل 1- مراحل ساخت الکترود گرافیتی
مشاهده میشود که ماده کربنی (کک سوزنی) پس از خردایش و عبور از سرند، در دانهبندیهای مختلف تقسیمبندی میشوند. سپس در مرحله بعد کک دانهبندیشده همراه با چسب (قیر) به خوبی مخلوط و اکسترود میشوند. به منظور افزایش خواص فیزیکی و کاهش تخلخل الکترود خام عملیات تلقیح (impregnation) انجام میشود که پس از آن فرایند گرافیتهکردن صورت میگیرد. امروزه جهت کاهش مصرف الکترود و جلوگیری از اکسیداسیون سطح الکترود مرحلهای دیگری به نام پوششدهی اضافه شده است.
بررسی بازار کک سوزنی در ایران و جهان
سه کشور آمریکا، چین و ژاپن بزر گترین تولیدکنندگان کک سوزنی در جهان هستند. کشورهای دیگری مانند هند، روسیه، آلمان و انگلیس از جمله کشورهای تولیدکننده کک سوزنی و الکترود گرافیتی در دنیا به شمار میروند.
عمدهترین مصرف کک سوزنی در ایران و جهان صنایع تولیدکننده فولاد با روش کوره قوس هستند. فولادسازی با کوره قوس عمدهترین روش تولید فولاد در ایران است به طوری که حدود ۸۵ درصد از کل فولاد تولید شده در ایران توسط کوره قوس تولید میشود. بر اساس گزارش انجمن جهانی فولاد در سال ۲۰۱۷ کل مقدار فولاد تولید ایران، ۲۱۷۰۰ هزار تن بوده است که تخمین زده میشود از این مقدار حدود ۲۳۰۰ هزار تن مربوط به تولید کوره بلند است. بنابراین ۱۹۴۰۰ هزار تن از ظرفیت تولید باقیمانده مربوط به کارخانجات دارای کوره قوس و القایی میشود. در ادامه اگر فرض شود که حدود یک میلیون تن فولاد از طریق کورههای القایی در کشور تولید شده است در نتیجه در سال ۲۰۱۷ میلادی، ۱۸۴۰۰ هزار تن فولاد توسط کوره قوس تولید شده است.
به طور کلی تخمین زده میشود که مصرف سالیانه الکترود گرافیتی در ایران (با فرض اینکه برای هر تن فولاد، ۲/۵ کیلوگرم الکترود مصرف شود) ۴۶ هزار تن است. در سند چشمانداز توسعه تولید فولاد ایران مشخص است که در سال ۱۴۰۴ میزان تولید فولاد کشور به ۵۵ میلیون تن میرسد. با توجه به اینکه حدود ۸۵ درصد فولاد کشور از تکنولوژی کوره قوس تولید میشود، بنابراین حدود ۴۷ میلیون تن فولاد از طریق کوره قوس تولید خواهد شد.
بنابراین در سال ۱۴۰۴ حدود ۱۱۷ هزار تن مصرف الکترود در ایران است که اگر فرض شود مبلغ هر تن الکترود حدود ۱۵۰۰۰ دلار شود در نتیجه حدود ۱.۷ میلیارد دلار باید صرف تأمین الکترود گرافیتی از خارج کشور شود. اگر فرض شود که در هر تن الکترود ۸۰ درصد آن را کک سوزنی و ۲۰ درصد دیگر را سایر افزودنیها تشکیل دهند؛ بنابراین نیاز به یک واحد ککسازی تأخیری با ظرفیت سالیانه ۹۳ هزار تن در سال است.
کشور چین به دلیل مقدار زیاد تولید سالیانه الکترود گرافیتی نقش به سزایی در بازار جهانی الکترود در صنایع فولاد بازی میکند که مشاهده شد در سال ۲۰۱۷ به دلیل سیاستهای کلان کشور در حوزه مسائل زیست محیطی صادرات الکترود گرافیتی چین به سایر کشورها به شدت کاهش یافته است. به بیان دیگر، چین با افزایش ظرفیت تولید فولاد کوره قوس و کاهش ظرفیت تولید فولاد کوره بلند در راستای رعایت مسائل زیست محیطی، حجم زیادی از مصرف کک سوزنی جهانی را به خود اختصاص داد و این موضوع باعث رشد شدید قیمت جهانی کک سوزنی شد.
همچنین افزایش تولید باتریهای لیتیمی مورد استفاده در خودروهای برقی در چین نیز عامل دیگر اختصاصدادن حجم زیادی از کک سوزنی به کشور چین محسوب میشود. در نتیجه در اواسط سال ۲۰۱۷ قیمت کک سوزنی طی ۳ ماه حدود ۴ برابر شد که باعث شده قیمت الکترود تا مرز ۲۵۰۰۰ دلار به ازای هر تن نیز افزایش یابد. متعاقب آن سایر کشورهای تولیدکننده جهت کنترل بازار ظرفیت تولید الکترود گرافیتی خود را افزایش دادند که باعث کاهش قیمت آن شد.
ایران جزء معدود کشورهایی است که با دارا بودن ذخایر نفت در واردات و صادرات کک نفتی نقش زیادی بازی نمیکند؛ در حالی که سومین کشور واردکننده الکترود گرافیتی است. صادرات الکترود گرافیتی به ایران که از ۵ کشور چین، دبی، هند، آلمان و اسپانیا صورت میگیرد. در مقابل، کشور ترکیه که فاقد منابع نفت خام میباشد وضعیتی مشابه ایران را در واردات الکترود گرافیتی دارد.
نتیجهگیری
از الکترود گرافیتی جهت اعمال جریان الکتریکی به منظور ایجاد قوس بین الکترود و مواد شارژ داخل کوره استفاده میشود که حدود ۸۰ درصد آن را کک سوزنی تشکیل میدهد. به دلیل عوامل نظری اکسیداسیون و عوامل مکانیکی الکترود در صنایع فولادسازی یک ماده مصرفی با نرخ به طور متوسط ۲.۵ کیلو برای هر تن فولاد به حساب میآید. اغلب شرکتهای تولید کک سوزنی از تکنولوژی ککسازی تأخیری استفاده مینمایند که بازده تولید کک در آن به کیفیت خوراک و عوامل فرایندی بستگی دارد.
در حال حاضر با توجه به تولید فولاد کشور که عمدتاً از طریق فرایند کوره قوس الکتریکی تولید میشود، به ۴۶ هزار تن الکترود گرافیتی و به تناسب آن ۳۷ هزار تن کک سوزنی مورد نیاز است. در صورت تحقق طرح توسعه تولید فولاد کشور تا سال ۱۴۰۴ که به ۵۵ میلیون تن میرسد، مقدار نیاز کشور به کک سوزنی ۹۳ هزار تن در سال است.
منبع: کتاب از نفت تا گرفت (مرجع تخصصی مسئله تولید الکترود گرافیتی و تولید کک سوزنی کشور)