گرافیت قالبگیری شده
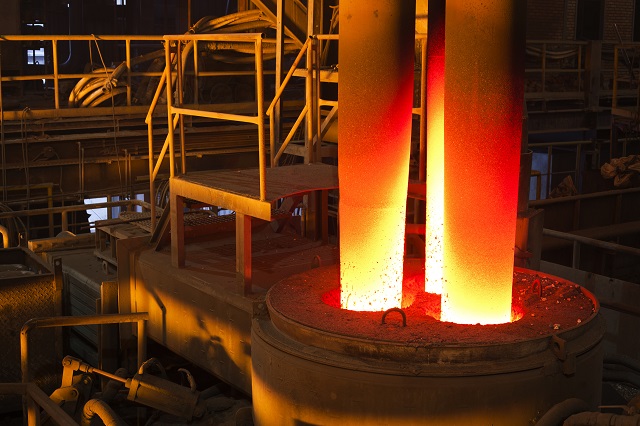
گرافيت قالبگيری شده (Molded Graphite) به منزلهی گرافيت مصنوعي شناخته ميشود که در اثر پرس کردن مخلوط کربن با چسبندهی آلي و سپس کربونيزاسیون و گرافيتيزه کردن به دست ميآید. اساس این فرایند در ابتدا با کوشش اچسن(Acheson. G. A) در سال 1896 اختراع شد. کاربرد اصلي گرافيت قالبگيری شده در الکترودهای استفاده شده در کورههای قوس الکتریکي و نيز در صنایع هستهای است. در حال حاضر گرافيت قالبگيری شده در گوشههای مختلفي از جهان در صنایع متنوعی استفاده ميشود.
فرایندهای گرافيت قالبگيری شده
- مواد اولیه
انتخاب مادهی اوليه ی مناسب جهت توليد گرافيت مرحلهی بسيار مهمي به حساب ميآید. چون اثر زیادی روی خواص و ارزش محصول نهایي توليد شده ميگذارد. بررسي دقيق خصوصيات مواد اوليه شامل: اندازهی ذرات، مقدار خاکستر کک، درجهی کربونيزه شدن قير، ساختار ذرات دوده و ميزان ناخالصي ذرات گرافيت طبيعي امری ضروری است. در کاربردهای هستهای گرافيت، داشتن کمترین ناخالصي و بيشترین خواص مکانيکي از خواص مهم گرافيت است که این امر نياز به انتخاب مواد اوليهی مناسب را هرچه بيشتر نشان ميدهد.
- فيلر(filler) یا پرکننده
فيلر معمولاً از موادی کربني انتخاب ميشود که به راحتي گرافيته ميشوند. عموماً از کک به جای فيلر استفاده ميشود که به منزلهی فيلر نرم شناخته ميشود و به سرعت در دمای 2700 درجه سانتیگراد، گرافیته میشود.
کک نفتي به جای فيلر در بيشتر کاربردهای صنعتي استفاده ميشود که به صورت یک محصول متخلخل از صنایع نفتي شناخته ميشود و در دمای اتاق به صورت کربن جامد وجود دارد. دیگر فيلرهای اصلي برای گرافيت مصنوعي الکترودهای بازسازی شده، گرافيت طبيعي و دوده هستند.
- چسبندهها (binder)
چسبندهها معمولا قير قطران زغالسنگ هستند که مادهای سخت، ترد و شيشهای است. این ماده با فرآوری کک متالورژی و با استفاده از تقطير یا عمليات حرارتي قطران زغالسنگ به دست ميآید. از هر تن متریک زغال 35 تا 60 کيلوگرم قير به دست ميآید.
دو فاکتور مهم روی خواص گرافيتاسيون قير مؤثر هستند:
- نقطهی نرمپذیری قير
- مقدار کینولین
نامحلول
این موارد در انواع مختلف قير متفاوت است. دیگر چسبندهها از جمله قير نفتي و رزینهای ترموستينگ برای کاربردهای ویژه استفاده ميشوند.
- خصوصيات گرافيت قالبگيری شده
گرافيت قالبگيری شده معمولاً با خواص زیر مشخص ميشود:
- دانسيتهی ظاهری
- مقاومت الکتریکي
- مدول یانگ
- ضریب انبساط حرارتي (CTE)
- استحکام خمشي
روشهای آزمایش خواص بالا و دیگر خواص گرافيت در جدول اشاره شده است:
ANSI/NEMA CB1-1977 ASTM C-886 | سختي (اسکلروسکوپ) |
ANSI/NEMA CB1-1977 ANSI C-64. 1 ASTM C559-79 ASTM C2080a ASTM C819-77 | دانسيتهی تخلخل |
ANSI/NEMA CB1-1977 ANSI C-64. 1 ASTM C651-70 (77) | مقاومت الکتریکي |
ASTM C695-75 | استحکام فشاری |
ASTM C749 -73 (79) | استحکام کششي |
ANSI/NEMA CB1-1977 | انبساط حرارتي |
ASTM C4561-69(79) | مدول الاستيسيته |
ASTM C562-69(79) | مقدار خاکستر |
ASTM C562 -69(79) | مقدار رطوبت |
دانسيته و تخلخل
دانسيتهی واقعي گرافيت قالبگيری شده یعني دانسيتهی تخلخل باز- که با پیکومتر اندازهگیری میشود- حدود 2.2 تا 2.3 گرم بر سانتیمترمکعب( است. این مقدار به دانسيتهی نظری 2.25 بسیار نزدیک است؛ یعنی حجم تخلخل داخلی بسیار کوچک است. دانسيتهی ظاهری گرافيت قالبگيری شده به ميزان تخلخل، نوع فرایند و سيکل اشباع سازی بستگي دارد؛ اما دانسيتهی واقعي در صنعت حدود 1.4 تا 2 گرم بر سانتیمترمکعب
( است. یکي از روشهای اندازهگيری دانسيته، روش آووگادو یا وزن-آب است. جهت جلوگيری از اشتباه در ميزان اندازهگيری تخلخل نمونه باید قبل از تست کاملاً خشک شود.
خواص مکانيکي:
استحکام و مدول
بررسي رفتار مکانيکي گرافيت قالبگيری شده بسيار مهم است. استحکام مکانيکي یک ماده تابعي از استحکام پيوند بين کریستالهای آن ماده است. شکست گرافيت قالبگيری شده در دمای محيط از نوع شکست ترد است.
بر خلاف بسياری از مواد، در گرافيت با افزایش دما، استحکام و مدول افزایش ميیابد. چون با افزایش دما، ساختار تبلور مجدد شده و تنشها آزاد ميشوند، در نتيجه ساختار عيوب آنيل ميشوند.
در دمای 2500 درجه سانتیگراد، استحکام گرافیت حدود 20 برابر دمای اتاق است. در بالاتر از 2500 درجه، تغيير فرم پلاستيک افزایش یافته و استحکام کاهش ميیابد. اثر دما بر استحکام و مدول گرافیت در شکل زیر نشان داده شدهاست:
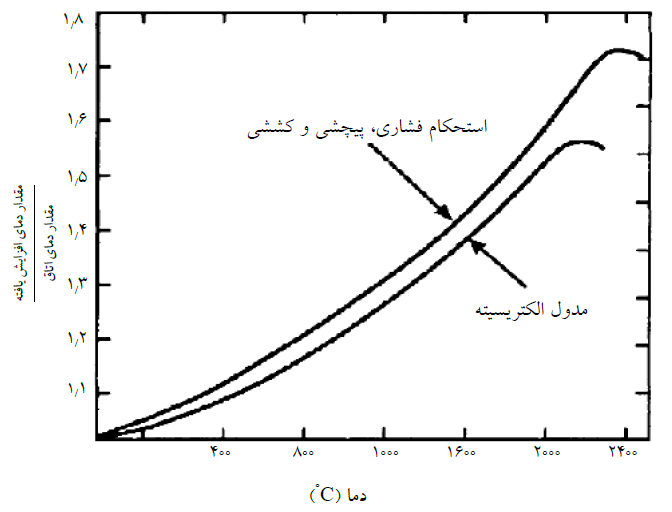
سختي
در کریستال گرافيت، فاصلهی ميان صفحههای اصلي نسبتاً زیاد است( nm0.343) و پيوندهای واندروالس ميان این صفحهها ضعيف است(7.1 Kj.mol).
دو روش اندازهگيری سختي گرافيت وجود دارد:
روش سختی تماسی – Contact Hardness
روش سختی اسکلروسکوپ – Scleroscope Hardness
جدول زیر سختي گرافيت و کربن قالبگيری شده را نشان ميدهد:
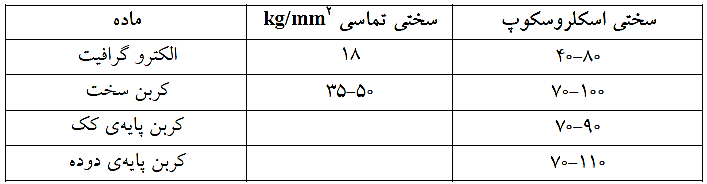
- فرایند توليد
مراحل تولید گرافیت قالبگیری شده در شمای کلی زیر مشاهده میشود:
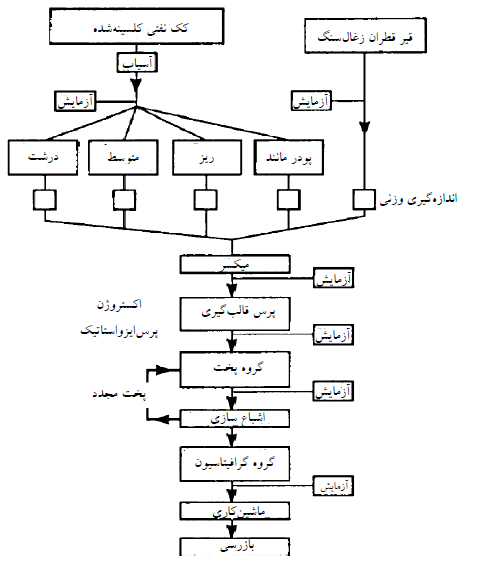
در مقالهای جداگانه به توضیح هریک از این مراحل زیر میپردازیم:
1.4 آسياب کردن
2.4 مخلوط کردن
3.4 تکنيک شکلدهي
4.4 کربونيزه کردن
5.4 مرحلهی اشباع سازی
6.4 مرحلهی گرافيتيزه کردن یا گرافيتاسيون
7.4 مرحلهی خالص سازی
8.4 ماشين کاری