گذری بر مهمترین روشهای ککسازی
کک نفتی ماده جامد نهایی غنی از کربن است که از فرایند پالایش نفت حاصل میشود و گروهی از سوختها به شمار میآید که به عنوان ککها شناخته میشوند.
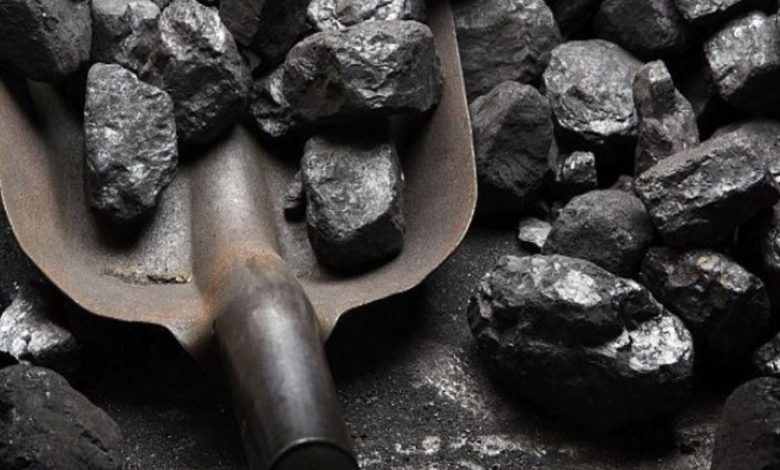
کک به عنوان ماده احیاء کننده و تامین کننده انرژی حرارتی لازم برای ذوب سنگ آهن در صنعت فولاد سازی کاربرد دارد. روشهای متنوع کک سازی سنتی و صنعتی بر اساس محدودیتها و ظرفیت تولید و معیارهایی مانند کیفیت و ابعاد کک تولیدی، میزان نرمه کک، میزان سرمایهگذاری، هزینههای جاری، نیروی کاری و قابلیت مکانیزاسیون، انتخاب میشوند. برای تولید کک از زغالهای خاصی استفاده میشود و همچنین خواص زغال سنگ تعیینکننده خواص کک است. کک دارای مواد غیر آلی زغال سنگ موسوم به استریل است که به صورت خاکستر باقی مانده و بر عملکرد کوره بلند موثر خواهد بود. وجود خاکستر منجر به افزایش مصرف کک و سنگ آهک در کوره بلند و کاهش ظرفیت تولید باتریهای کک سازی میشود .
روشهای کک سازی
فرایند کک سازی تبدیل باقیماندههای سنگین به کک و مواد دیگر را ممکن میسازد. این فرآیند بیشتر در مناطقی مطرح میشود که از سوختهای سنگین استفاده چندانی نمیکنند و در نتیجه باقیماندههای سنگین بیمصرف میمانند. در این حالت میتوان از فرآیند کک سازی استفاده کرد که در واقع یک شکست حرارتی شدید است.
فرآوردههای کک عبارتند از: کک، گاز، بنزین و گازوئیل که معمولا به عنوان خوراک شکست کاتالیستی و نیز هیدروکرکینگ به کار میرود.
کُک به دو روش قابل تولید است، که در ادامه به آنها میپردازیم.
- استفاده از زغال سنگ (کک زغال)
- استفاده از پسماندهای نفتی (کک نفتی)
استفاده از زغال سنگ (کک زغال): با حرارت دادن به زغال سنگ، میتوان آن را به مواد مفیدی برای استفاده در صنایع تبدیل کرد. انواع مختلف زغال سنگ، با توجه به نوع آن و شرایطی که ازلحاظ دما و فشار در آن قرار میگیرد، به مواد گوناگونی تبدیل میشود. معمولا بهطور کلی، زغال سنگها در دمای حدود ۱۰۰ درجه سانتیگراد رطوبت خود را از دست داده و نهایتا تا دمای 400 درجه سانتیگراد تجزیه شده و مقادیر مختلفی از مواد روغنی و گازی شکل تولید میکنند. پس از تبدیل زغال سنگ، مواد فرار آن خارج شده و محصول نهایی کک با درصد بالای کربن به دست میآید.
استفاده از پسماندهای نفتی (کک نفتی)
کک سازی تاخیری
از نظر آماری، امروزه برای فرآوری مواد باقیمانده، بیشتر از روش کک سازی تأخیری استفاده میشود. با وجود مقبولیت این واحد، تعداد کمی سازنده و پالایشگر دانش طراحی کک سازی تأخیری را دارند. کک سازی تأخیری یک فرآیند شکست گرمایی شدید است که در پالایشگاههای نفتی برای بهبود و تبدیل ته ماندههای نفتی به مایعات، گازها و کک نفتی به کار میرود. برای رسیدن به دمای مناسب شکست گرمایی (505-485 درجه سانتیگراد) از لولههای بزرگ عمودی که با مشعل گرم میشوند، استفاده میگردد. زمان ماندن در کوره بسیار کوتاه است و کک سازی تا زمانی که خوراک به درامهای بزرگ کک سازی برسد به تعویق میافتد. این فرایند به صورت نیمه مداوم انجام میگیرد در حالی که جریان خوراک مداوم است؛ اما جداسازی کک تولید شده به صورت دورهای انجام میشود. جریان خوراک بین یک یا چند عدد درام تغییر میكند. یک درام به صورت لحظهای با خوراک پر شده و درام دیگر سرد میشود. ککهای موجود در آن به صورت هیدرولیک جدا شده و سپس دوباره گرم میشود. در شکل زیر شماتیک فرآيند کک سازی تأخیری نشان داده شده است.
فلکسی کک
خوراک این فرایند میتواند هر نوع نفت سنگینی باشد. خوراک ابتدا حدود 315 تا 370 درجه سانتیگراد پیش گرم شده و به درون راکتور اسپری میشود تا با بستر داغ و سیالی کک در تماس قرار بگيرد. این کک داغ از گرمکن کک (با نرخ جریانی که راکتور را به صورت سیالی نگه دارد) بین 510 تا 540 درجه سانتیگراد به راکتور بازگردانده میشود. کک بازگشتی از گرمکن کک، حرارت کافی برای تبخیر خوراک و واکنش شکست را فراهم میكند. بخار شکسته شده از سیکلون عبور میكند و سپس در اسکرابر بالای راکتور خنک میشود.
برخی از بخارات سنگین در اسکرابر میعان یافته و به راکتور باز میگردند. کک تولید شده در شکست به صورت فیلم نازک بر روی سطح ککهای موجود مینشیند. در پایین راکتور، کک با بخار جدا میشود تا محصولات واکنش با کک خروجی از راکتور ترکیب نشوند. کک از راکتور به سمت گرمکن در دمای حدودا 593 درجه سانتیگراد جریان مییابد. گرمکن کک نیز یک تجهیز بستر سیال است. در ادامه جریان کک وارد سومین بستر سیال میشود و در آنجا با هوا و بخار برای تولید یک گاز شامل کربن مونوکسید، هیدروژن، کربن دی اکسید و نیتروژن، واکنش میدهد. سیستم به گونهای طراحی شده که محصول کک در این راکتور بین 60 تا 97 درصد گازی سازی میشود. ارزش حرارتی گاز کک تولیدی، از گاز طبیعی کمتر است. در زیر دیاگرام جریانی سادهسازی شده فلکسی کک را مشاهده میکنید.
کک سازی سیال
ککسازی سیال روشی ساده از نسخه فلکسی کک سازی است. در این روش کک گازی سازی نمیشود. بنابراین تنها دو بستر سیالی شده وجود دارند. کک سازی سیال روش جدیدتری است ولی عیب آن تولید کک پودری شکل که کاربرد آن توأم با اشکال است. خوراک ابتدا حدود 300 درجه سانتیگراد گرم شده و وارد راکتور میشود. در راکتور کک به صورت بستر سیال داغ وجود دارد و دمایش حدود 450 درجه سانتیگراد است. شکست خوراک بلافاصله پس از ورود به راکتور انجام شده و مقدار زیادی کک تشکیل میشود که بر روی ذرات کروی کک موجود در راکتور رسوب میكند. این ذرات به طور مداوم از پایین راکتور خارج و به یک گرمکن فرستاده میشود. در آنجا قسمتی از کک (حدود 5 درصد) به کمک جریان هوا سوزانده شده و به این ترتیب دما تا 620 درجه سانتی گراد بالا میرود. قسمت اعظم کک دوباره به راکتور برگردانده میشود و بقیه آن که میزان کک خالص است، از پایین گرمکن خارج شده و پس از سرد شدن با آب به انبار فرستاده میشود. فرآوردههای سبک خروجی از بالای راکتور وارد یک ستون تفکیک کوچک شده و در آنجا گاز و بنزین و گازوئیل از یکدیگر جدا میشوند. شماتیک کک سازی سیال در تصویر زیر آورده شده است.
منابع:
- کتاب جامع از نفت تا گرفت؛ مسئله الکترود گرافیتی
- https://civilica.com/doc/331145/certificate/print
- https://www.entakala.com/blog/coke